Capabilities
Aerospace Composites facility was established in 2018 to complement the existing metallic capabilities to cater to the growing demands in Aerospace sector. The facility is laid out on nearly 7450 square meter area in U-flow pattern to facilitate smooth process flow integrating all activities from storage of raw material to assembly of large structures under one roof. The facility has been comprehensively planned to provide industrial partnership to the Space, Defence and Aviation endeavors of the country as well as to compete in Global Aerospace Arena.
ATC Composites facility has been accredited with AS 9100D and NADCAP. Highly proficient and experienced human resource in composite manufacturing adds to the core strength of our organization. LMW composites team is being equipped to Design, Develop, Qualify and Manufacture the structural products from given configurational definition and load spectrum.
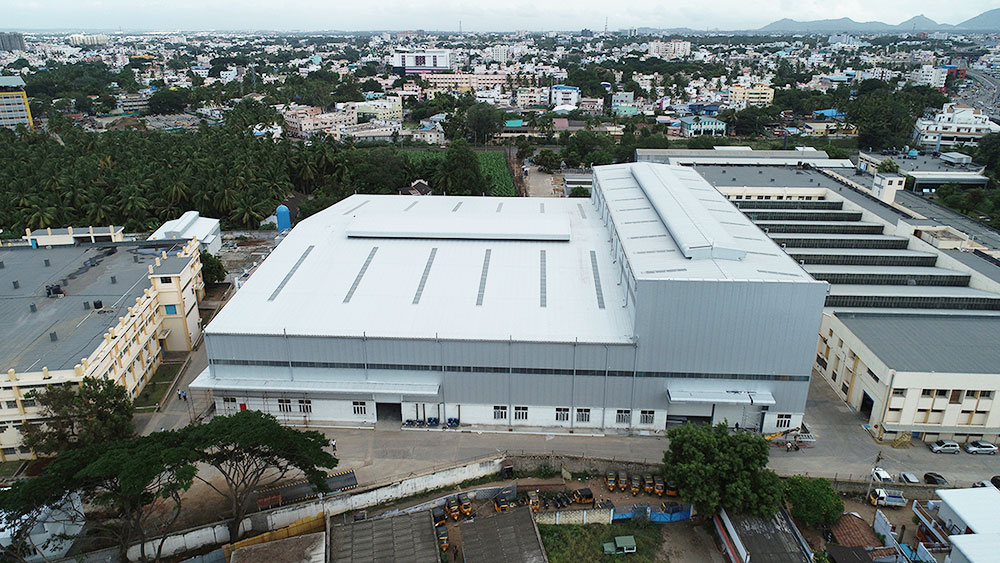
Major Highlights
The State-of-the-Art facility is comprehensively equipped to manufacture structural composites parts, sub-assemblies and assemblies for Aerospace and Defence applications. The Facility is equipped with
- Cold storage (-20℃ ± 2℃)
- Clean Room – Low Bay: Height – 6m, Area: 400 square meters, ISO Class 8 (Convertible to ISO Class 7)
- Clean Room – High Bay: Height – 12m equipped with 10T EOT Crane. Area: 600 square meters, ISO Class 8
- Universal Testing Machine: Capacity – 100kN
- CNC Prepreg Cutting Machine
- Autoclave 1: 1.3 m Dia and 2.4 m length, Temperature: 450℃, Pressure: 15 Bar
- Autoclave 2: 4 m Dia and 6 m length, Temperature: 250℃, Pressure: 10 Bar
- NDT: Sophisticated C-Scan from Scan Master – 10 Axis : Dry & Wet probes of size 7m x 2m x 3m
- NDT: A-Scan, Phased Array Ultrasonic Testing equipment
- Resin Transfer Moulding & Vacuum Infusion Moulding
- High assembly bay of 1870 square meters (Size – 85 m x 22 m x 22 m) equipped with two cranes, 10T crane at 18m level and 5T crane at 10m level
- Hot Air Oven: Size – 6 m x 4 m x 3.5 m
Facility
Product Portfolio in our vision
Space and Defence Components
- Pay load fairings
- Composite interstage structures
- Radomes for space, airborne and ground applications
- Antenna reflectors
- Solar panel substrates
- Pressure vessels
- Motor cases
- Missile launcher tubes
Fixed-Wing Aircraft Components
- Fuselage components
- Fin and Rudder
- Interior components
- Floor beams and panels
- Fixed wing structures
- Flaps, Ailerons and Spoilers
- Engine nacelles
Rotary-Wing Aircraft Components
- Main rotor blade and Hub plate
- Tail rotor blade and Hub plate
- Door assembly and interiors
- Engine cowlings
- Landing skids
- Empennage components